Foam VS Fiberglass, what do you need to know?
FACE for professionals
FACE for MI Resellers
FACE Project Integration
One of the reasons being, not only because of its efficient absorption properties, but also it’s good looks.
The thing is, cutting, shaping, and wrapping panels in fabric was extremely costly… beyond what the classic home studio could afford. There needed to be a low-cost alternative. It just so happens that the lightweight and cheap polyurethane foam was there to fill the need. So, what are the differences between these materials when used in absorptive acoustic panels you ask?
Function
The average density of foam is less than 1.6 lbs per cubic foot. A block of foam is cut into 2 pieces to resemble some type of anechoic wedge pattern. Many people have been led to believe that these patterns improve the performance of the panel, but that is incorrect. This is really only a creative way to cut 2 panels from a single block of foam, which effectively reduces the density by 50%! Primacoustic Broadway fibreglass panels share the same density specification as the industry standard “705” panel: 6 lbs per cubic foot, or almost 4 times the density of foam. This higher density material absorbs high frequencies just as well as the lightweight foam, but keeps working at low frequencies. Both panels work well at higher frequencies, but things quickly change as the frequency is lowered.
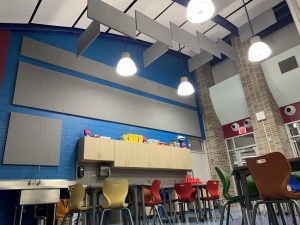
Installation
The installation methods can make or break a project. Foam panels are generally installed using adhesives that often permanently deface the wall surfaces and eliminate the possibility of re-using the treatment in another space. Fibreglass panels are installed using impaler clips. It is a quick & easy installation and can be completed by one person as panels move easily, and minimal damage to the wall surface typically occurs.
Safety
In 2003, after an unfortunate incident in Rhode Island, Fire Marshals all over North America were suddenly interested in what was being installed on the walls of commercial & public occupancy buildings, as certain paneling was at fault for fires in the area. It was found that polyurethane foam paneling installed was to blame. Acoustic foam panels typically meet the “California-117” or “Class B” ratings for fire resistance, which no longer meet building codes or insurance requirements in most areas. Broadway fibreglass panels meet the stringent criteria required to achieve “Class 1” or “Class A” fire ratings. These standards were developed by the ASTM as a way of classifying building materials. This is why we are such big fans.
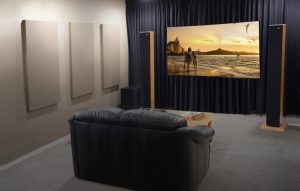
Cost
As the price we pay at the pumps has increased over the years, so has the price of the oil based chemicals used to produce acoustic foam in turn. Polyurethane foam is an oil-based material. With foam becoming so costly, we at Primacoustic asked ourselves how we could produce fibreglass panels affordably. The answer? Limit the available colors & sizes. Having a mass production and simple inventory equals a lower cost for our customers who are on the hunt for something that will really do the trick.
Look
There is a reason that we rarely see foam in the professional studio as foam degrades over time. The panels collect dust, fade, crumble, and are impossible to clean. Fibreglass panels are manufactured with a resin hardened edge that maintains a crisp shape and appearance without breaking down. The fabric covering has a professional appearance that looks great in any environment and can be easily cleaned with a vacuum.
As we noted, fibreglass panels look great, last for years, and can be installed anywhere safely while adhering to fire codes and alleviating liability concerns. The tests show that the performance of Broadway fibreglass panels greatly exceeds that of the foam. Superior acoustic performance over a wider frequency range means less material is required to treat a larger space… We suggest Broadway as the cost effective choice!
Nothing is a one-size-fits-all solution. That’s why we have a specialized team of trained acousticians who are available to give you a custom product offering that addresses your specific needs. We are happy to help assist you with anything you need. Feel free to contact Neel Swinnen.